Gleeble® Systems: A Complete Family of Research Tools to Improve Materials, Optimize Processes & Increase Profits
Gleeble systems are available in several models, each with a wide variety of available options and configurations. This flexibility allows the tailoring of a Gleeble system to meet your exact testing requirements. Available options include transducers, load cells, contact and non-contact extensometers, infrared pyrometers, quench systems, jaws, grips and vacuum systems.
The most popular machines are the Gleeble 3180-GTC, Gleeble 3500-GTC and Gleeble 3800-GTC. Mobile Conversion Units (MCUs) are available for 3500-GTC and 3800-GTC models which provide application-specific capabilities. MCUs include the Hydrawedge, MAXStrain, Hot Torsion and the new Ultra High Temp System. Gleebles can also be modified to conduct testing in beam lines and can be equipped with a Laser Ultrasonic Measurement System (LUMet) for real-time microstructure monitoring.
Additionally, Dynamic Systems Inc. has launched the Gleeble 500 Series - an all-new lineup of research systems optimized for performance, versatility and value. Requiring a lower investment than the traditional 3000 Series systems, the Gleeble 500 series of systems, including the Gleeble 563, Gleeble 540, and Gleeble 525 are tailored to provide compact, economical solutions for researchers while retaining the world class capabilities that have made Gleeble systems the industry standard.
This flexibility allows the tailoring of a Gleeble system to meet your exact testing requirements. The chart below lists popular Gleeble systems with key specifications and a comparison of applications and research capabilities. A more detailed comparison of Gleeble systems is available here.
Click here for a comparison of our most popular systems.
GLEEBLE SYSTEMS
Gleeble 3800 - Extending the State of the Art in Physical Simulation
Building on the success and capabilities of the 3500, the Gleeble 3800 is designed to offer capablities for hot deformation simulations on large specimens and is equipped with a heavy-duty mechanical system and high-speed servo valves for quick response.
Through its powerful physical simulation capabilities, the Gleeble 3800 delivers the technical leverage that competitive organizations need to cut costs, shorten time to market and open the door to new ideas. The Gleeble 3800 is similar to the Gleeble 3500 in terms of applications served, however the Gleeble 3800 is capable of exerting as much as 20 tons of static force in compression and up to 10 tons of force in tension. Stroke displacement rates can be programmed to be as fast as 2000 mm/seconds.
The 3800 is ideally suited for the following applications:
• Hot Tensile Tests
• CCT and CHT (with deformation)
• Continuous Casting Simulation
• Weld HAZ Simulation
• Melting and Solidification
• Heat Treatment
|
• Mushy Zone Processing
• Hot Rolling
• Forging
• Extrusion
• Upset Butt Welding
• Diffusion Bonding
• Continuous Strip Annealing
• Quenching
• Powder Metallurgy/Sintering
• Synthesis (SHS)
|
Click here for more information and specifications.
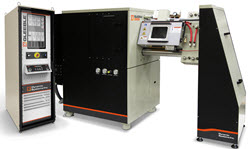
Like the Gleeble 3180, the Gleeble 3500 is a fully integrated digital closed-loop control thermal and mechanical testing system. The 3500 adds increased mechanical capabilities enabling researchers to study the impacts of up to 10 tons of static force in tension or compression, with displacement rates as fast as 1000/mm/second. The direct resistance heaing system of the Gleeble 3500 can heat specimens at rates of up to 10,000°/second and can hold steady-state equilibrium temperatures.
The 3500 is ideally suited for the following applications:
• Hot Tensile Tests
• CCT and CHT (with deformation)
• Continuous Casting Simulation
• Weld HAZ Simulation
• Melting and Solidification
• Heat Treatment
|
• Mushy Zone Processing
• Hot Rolling
• Forging
• Extrusion
• Upset Butt Welding
• Diffusion Bonding
• Continuous Strip Annealing
• Quenching
• Powder Metallurgy/Sintering
• Synthesis (SHS)
|
Click here for more information and specifications.
Gleeble 3180 - The Economical Standard for Physical Simulation and Thermal-Mechanical Testing
The ideal solution for both the research lab and production floor, the Gleeble 3180 replaces the Gleeble 1500 as a cost-effective Thermal-Mechanical Simulation System with broad capabilities applicable to the testing and simulation needs of multiple industries.
The 3180 is ideally suited for the following applications:
• CCT and CHT (with deformation)
• Continuous Casting Simulation
• Weld HAZ Simulation
• Melting and Solidification
• Heat Treatment
Click here for more information and specifications.
Gleeble 563 - Thermal Mechanical Simulator As the most capable member of the Gleeble 500 Series, the Gleeble 563 is tailored to provide a compact, economical solution for researchers while retaining the world-class capabilities that have made Gleeble systems the industry standard. Click here for more information and specifications. |
![]() |
|
Gleeble 540 Welding Simulator - A complete platform for a wide range of welding simulations and testing capabilities The new Gleeble Welding Simulator has been designed from the ground up with the needs of welding researchers in mind. The capabilities of this system are customized to meet those needs. It has been tailored to provide a compact, low cost solution while retaining world-class capabilities that have made Gleeble systems the industry standard. Click here for more information and specifications. |
![]() |
|
Gleeble 525 - Strip Annealing Simulator
A Dedicated Simulation System for Optimizing Continuous Annealing, Galvanizing and Coating Lines The Gleeble 525 Strip Annealing Simulator is a low-cost system built specifically for simulating thermal cycles in sheet specimens, including continuous annealing line, batch annealing, Quenching and Tempering (Q+T), Quenching and Partitioning (Q+P) and other heat treatment processes. Click here for more information and specifications. |
![]() |
MOBILE CONVERSION UNITS (MCUs) (Available on Gleeble 3800 or Gleeble 3500 models)
MAXStrain® Multi-Axis Hot Deformation System - A research tool for making ultrafine-grain and nano materials
The MAXStrain multi-axis hot deformation system is a unique research tool that can subject materials to virtually unlimited strain under precise control of strain, strain rate, and temperature. The system restrains specimens lengthwise while allowing unlimited deformation in the other two dimensions. As a result, very high strain levels can be introduced into specimens to produce a sample of ultrafine-grain or nanoscale material that is large enough for subsequent properties testing.
The MAXStrain system can be used on steels, aluminum alloys, titanium, and other metals.
Because the MAXStrain provides unparalleled, accurate control of all parameters, it offers a high degree of reproducibility. Researchers quickly and precisely create materials in the laboratory under well controlled mechanical and thermal conditions.
The MAXStrain is only available on Gleeble 3800 systems.
Click here for more information and specifications.
Hot Torsion System - Modern hot torsion with high-speed thermal capability
The Hot Torsion system is available as a standalone machine or as an option for use with Gleeble 3500 and 3800 physical simulation systems. The Hot Torsion system incorporates a number of new and innovative designs.
Capable of applying torque up to 100 Nm, the Hot Torsion system is the first commercially available torsion testing system to incorporate a direct resistance heating system. In addition, the system features the following capabilities:
• Rapid, uniform direct resistance heating of samples
• Heating of test specimens at any time during torsion
• Rapid in-situ quenching of the test specimen at any point in the test (direct resistance heating only)
• Can use air, water or mist for quench media
• Can apply controlled tension axially during torsion
• Torsion tests can be conducted with full axial restraint or no axial restraint
• High-speed hydraulic torque motor for rapid strain rate changes
• Variable torsion coupler for higher acceleration speeds
• Free coupler minimizes strain error during specimen loading
• Optional specimen furnace available
Click here for more information and specifications.
Hydrawedge II® - The ultimate tool for optimizing hot rolling and forging processes
For researchers who wish to optimize multiple-hit, high-speed deformations— including multi-stand rolling mills and multi-hit forging processes—the Hydrawedge offers excellent physical simulation capabilities.
Available as a stand-alone machine or as an option for the Gleeble system, the Hydrawedge is the only commercially available machine that offers the capability to perform high-speed deformation simulations with complete independent control of both strain and strain rate.
Click here for more information and specifications.
High Temperature Testing - Enhanced capabilities for exceptional performance
All Gleeble systems are capable of simulations at elevated temperatures. For applications that require high temperatures (1800-2000°C) for extended periods of time, the High Temperature Mobile Conversion Unit offers enhanced capabilities to accommodate more demanding requirements. The unit is loosely based on the General Purpose MCU which allows for the use of standard specimen grips and accessories.
The High Temperature Testing MCU is compatible with 3500 and 3800 systems.
Features include:
• Vacuum tank for atmosphere control
• Modified view port for improved safety and functionality
• Available with higher temperature pyrometers
• Additional groundingh paths for improved resistive heating
• Increased water cooling
Click here for more information and specifications.
SPECIALTY MACHINES
Strip Annealing System - Controlled heating and cooling cycles on large sheet samples with large uniform temperature zones.
The new Large Sample Strip Annealing Mobile Conversion Unit (MCU) is designed to provide controlled heating and cooling cycles on large sheet steel samples for replicating the heating and cooling cycles of sheet annealing processes. The sample size is large enough to provide subsequent properties testing of the material.
The MCU is equipped with the following:
• Vacuum tank for atmosphere control
• Spray heads and valve controls for air and air/water mist quenching of sheet metal specimens
• Quench valve controls are integrated for control with the Gleeble computer
• Pneumatic grips for easy loading/unloading and consistent clamping pressures
• Grips for use with steel specimens
• Feed through for 4 thermocouples
Click here for more information and specifications.
LUMet® - Laser Ultrasonic Sensor for In-Situ Metallurgical Microstructure Studies
It is now possible to monitor metallic microstructures in real time, in-situ, and at high temperatures while conducting physical simulations on a Gleeble, thanks to laser-ultrasonics.
Days and weeks of metallurgical studies yielding a few measurements on quenched samples can often be replaced by a single in-situ laser-ultrasonic test, yielding hundreds of measurements in real time.
Real-time, in-situ measurement of:
• Recrystallization
• Grain Growth
• Grain Size
• Phase Transitions
• Elastic Constants
Laser-ultrasonics is a technology that enables non-contact ultrasonic measurements, using lasers to generate and detect ultrasound pulses. Unlike other ultrasonic technologies, it can be used on hot materials up to any temperature because there is no physical contact. Therefore, it is ideally suited for in-situ studies of solid metallic or ceramic materials up to their melting point.
Click here for more information and specifications.
HDS-V40 Direct Rolling Simulator
The only commercially available laboratory system capable of simulating direct rolling, from the continuous caster to the end of the hot rolling process, all in one continuous sequence using a single specimen.
For the first time ever, steel makers can explore the promise of continuous casting and direct rolling (CC-DR) on an affordable, reproducible laboratory scale. In addition to direct rolling, this system can be used for simulating semi-solid rolling (liquid metal core reduction), plane strain compression, hot rolling and forging.
The HDS-V40 has two 40-ton hydraulic systems—opposed to each other—that deform the specimen in equal amounts for true plane strain deformation. Maximum stroke rate is 1.7 meters per second; minimum stroke rate is 0.1 millimeters per second. Each mechanical system is equipped with its own internal Hydrawedge‚ for precise control of strain and strain rate. Through another servo-hydraulic system, the HDS-V40 also can precisely control expansion and contraction of the material as it melts and solidifies to provide a more accurate simulation.
Click here for more information and specifications.
A new Gleeble physical simulation system, designed specifically for use in a synchrotron has been developed and can be used for multiple applications.
The first 'Beam Line Gleeble' was installed at the Brazilian Synchrotron Light Laboratory (LNLS). The system is being used to perform advanced and unprecedented in-situ materials studies combining the power of high flux x-ray beam emanating from the synchrotron source and the dynamic thermo-mechanical capabilities of a Gleeble simulator, which make it possible to unveil the fundamentals of structural and functional materials behavior when subjected to specific thermo-mechanical conditions.
Click here for more information and specifications.